Integration von 2 optischen Sortiermaschinen von Sortop Potatoes in eine bestehende Linie bei Warnez in Belgien
Ein Projekt in Zusammenarbeit mit DeprezDeprez installierte bei Warnez ein neues System mit zwei optischen Sortiermaschinen von Visar Sorting, während die Produktionslinie weiterlief und der Standort zuvor unzugänglich war. Lesen Sie weiter, um zu erfahren, wie das Ganze abgelaufen ist.
Beschreibung des gesamten Projekts
und Empfehlungsschreiben
Die Ausgangslage
Bei der Kartoffelverpackungsfirma Warnez wurden die gewaschenen Kartoffeln mit optischen Sortiermaschinen von Newtec Celox sortiert. Die Kartoffeln werden dann in Kisten verpackt und im automatischen Lager bis zur Verpackung gelagert. Falls erforderlich, werden die Kartoffeln auf dem Inspektionstisch einer letzten Kontrolle unterzogen, bevor sie an die Verpackungslinie weitergeleitet werden. «Zurzeit geschieht dies auf fünf Inspektionstischen, die jeweils mit zwei Personen besetzt sind, so dass wir in diesem Bereich ständig zehn Personen beschäftigen», sagt Mathias Mergaert, Vertriebsingenieur bei Deprez. «Ursprünglich wurden wir gebeten, eine automatisierte Alternative für nur einen der Inspektionstische vorzuschlagen. Es war auch ein mechanischer Sortierer vorhanden, der aber nicht immer den Anforderungen von Warnez entsprach. Auch das wollten wir verbessern, und deshalb haben wir ein neues Projekt mit breiteren Möglichkeiten gestartet.»
Die Lösung
Um die Qualität des Endprodukts besser überwachen zu können, wurde beschlossen, den vorhandenen Schüttelsortierer zu ersetzen, und es wurden zwei optische Sortierer von Visar in der Produktionslinie installiert. Während der Inspektionsphase ist es möglich, beide Visar Sortop Potatoes gleichzeitig zu betreiben oder nur einen von ihnen. «Wir freuen uns immer, wenn unsere Partner uns Vorschläge machen, wie wir noch besser werden können. Unsere Geschichte wurde sofort aufgegriffen und wir konnten sofort große Schritte machen», sagt Kurt De Nys, CEO von Warnez.
Die Installation der optischen Sortiermaschinen von Visar eröffnet zusätzliche Möglichkeiten bei der Sortierung. Mathias Mergaert erklärt: «Während der Rüttelsortierer nur in fünf verschiedene Größen sortieren konnte, können diese optischen Maschinen in fünf verschiedene Klassen sortieren, wobei die Qualität und das Kaliber berücksichtigt werden. Wir können auch flexible Kombinationen definieren, oder es gibt die Möglichkeit, nur gut/schlecht einzustellen.» All dies bedeutet, dass die Integration von optischen Sortierern in das System dazu beiträgt, die Qualität des Endprodukts zu gewährleisten. Die Geschwindigkeit, mit der die Anlage die Inspektion durchführen kann, hängt von den Eigenschaften der Kartoffeln ab, wobei die Sortierkapazität bei relativ großen Kartoffeln 20 Tonnen/Stunde beträgt.
Um den Warnez-Mitarbeitern ein angenehmes Arbeitsumfeld zu bieten, wurde jede der beiden Visar Sortop Potatoes-Maschinen in eine eigene Kammer eingebaut, um eine maximale Geräuschdämpfung zu gewährleisten. Da der Bereich täglich gereinigt wird, war Edelstahl die logische Wahl.
Der Ablauf
«Die größte Herausforderung bei der Umsetzung war der Bereich, in dem die Arbeiten durchgeführt wurden. Mit dem derzeitigen Installationsmaterial war es nicht möglich, ihn von innen zu erreichen. Die Lösung war das Dach», erklärt Projektleiter Yannick De Geeter. «Der Arbeitsbereich wurde mit Planen abgesperrt, um die Produktionshalle von Baustellenstaub und Regen freizuhalten. Dann wurden die Dachplatten entfernt. Auf diese Weise wollten wir den Schüttelsortierer ausbauen und die neuen Maschinen einbringen. Selbst mit diesem Plan hatten wir noch Probleme mit dem Zugang. Der Kran musste eine bestimmte Tragkraft haben, und selbst die breiteste Stelle des offenen Daches hatte nur eine schmale Öffnung. Also mussten wir uns nach dem richtigen Turmkran umsehen.
Kurt De Nys, CEO von Warnez Potatoes, erzählt die Geschichte weiter: «Wir arbeiten schon seit vielen Jahren mit Deprez zusammen und wissen, wie viel Erfahrung sie haben, also waren wir zuversichtlich. Und wir hatten Recht», sagt er. «Man könnte sagen, dass wir eine Operation am offenen Herzen am Fließband durchführten und gleichzeitig eine Verjüngungskur machten. Das bedeutete, dass eine offene Kommunikation sehr wichtig war – sowohl mit dem Deprez-Team als auch mit unseren eigenen Sicherheits- und Qualitätsabteilungen. Wir haben auch technische Mitarbeiter in unserem Unternehmen, und die Übergabe an sie verlief ebenso reibungslos.»
Die Öffnung des Daches war nicht ganz ohne technische Herausforderungen. Dort befanden sich Solarpaneele, was bedeutete, dass es nicht wirklich möglich war, ein Loch an der offensichtlichen Stelle zu machen. «Wir konnten den Bereich, in dem die Installationen enden sollten, nicht vollständig öffnen. Wir mussten elektrische Gabelstapler hineinziehen, damit wir an den unzugänglichen Stellen installieren konnten», sagt Yannick. «Da der Arbeitsbereich so beengt war und wir auf mehreren Ebenen bauten, musste sichergestellt werden, dass alle Arbeiten in der richtigen Reihenfolge ausgeführt wurden. Das System ist an sich schon ziemlich komplex, daher war es wichtig, dass wir uns Gedanken darüber machen, wie wir es angehen. Die Produktionslinie verfügte bereits über Kistenbefüller. Die Ausgänge des Visar konnten perfekt an das bestehende System angeschlossen werden.
Um ohne Unterbrechung weiterarbeiten zu können, musste auch das Wetter passen. «In der Produktionshalle lief die Arbeit ununterbrochen weiter. Auf Regen konnten wir sowohl bei der Produktion als auch bei der Installation verzichten! Leider gab es zwei Nächte, bevor alles fertig war, einige Regenschauer. Wir waren froh, dass die Planen unsere Produktionsumgebung erfolgreich vor dem Regen geschützt haben. Die Anlage selbst war so konzipiert, dass sie mit Wasser bespritzt werden konnte, sie hatte also sozusagen eine Art Feuertaufe zu bestehen.
Einige der demontierten Maschinen wurden zur Aktualisierung und Modifizierung an unseren Standort in Kortemark zurückgeschickt. Dank einer sorgfältigen Planung verlief die Umsetzung der neuen Anlage sehr gut, und wir konnten den Zeitplan sogar noch übertreffen! Wir übernahmen die Verantwortung für alle Installationsarbeiten. Es dauerte zwei Wochen, bis die Arbeiten abgeschlossen waren, und dann haben wir das Dach wieder abgedichtet.
«Als wir feststellten, dass die einzige Möglichkeit, das neue System effizient zu installieren, darin bestehen würde, das Dach abzunehmen, begann ich mich zu fragen, ob das Projekt funktionieren würde», berichtet De Nys. «Wie sich jedoch herausstellte, wurde das Projekt drei Wochen vor dem Termin fertiggestellt, so dass der Plan tatsächlich hervorragend funktionierte!»
Das Ergebnis
Alles wurde innerhalb eines relativ engen Zeitplans installiert. Der effektive und effiziente Demontage- und Montageprozess gewährleistete die Kontinuität der Produktion des Kunden. Deprez ist es gelungen, durch dieses anspruchsvolle Projekt einen Mehrwert für Warnez zu schaffen. Während die Verpackungslinie in Betrieb blieb, wurden die internen Systeme aufgestockt. Der mechanische Sortierer wird von Deprez in der Kartoffelannahmestelle nachgerüstet.
«In den ersten Wochen des Produktionsprozesses stellten wir schnell fest, dass die Kapazität für kleine Kartoffeln oder Babykartoffeln weit über den geplanten 2,5 Tonnen/Stunde lag. Tatsächlich erreichten wir schon recht früh 4 Tonnen/Stunde!»
«Die optische Sortierung funktioniert so gut, dass wir jetzt überzeugt sind, dass wir alle Inspektionstische ersetzen wollen, sobald wir können. Das ist vielleicht ein Präzedenzfall in der Kartoffelverpackung, aber Tests haben gezeigt, dass wir den Abfall um 30 % reduzieren können, wenn wir zu optischen Sortierern wechseln», sagt Kurt De Nys. «Dank all der guten Arbeit, die unsere Bediener an den Inspektionstischen leisten und geleistet haben, wird es kein großer Schritt sein, auf eine vollständige Automatisierung umzustellen. Sowohl aus menschlicher als auch aus betriebswirtschaftlicher Sicht ist der Austausch der Prüftische eine echte Optimierung des Produktionsprozesses. Es ist nur eine sehr kurze Zeit vergangen und wir sehen bereits Kosteneinsparungen», schließt der CEO.
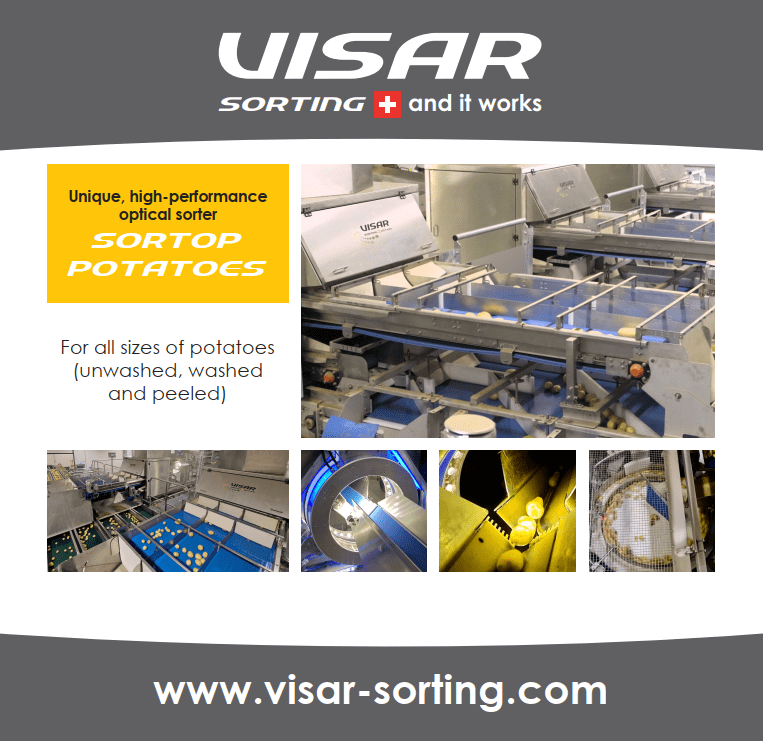